Music Career Finder
Survey Start
Instrument Repair and Restoration Specialist
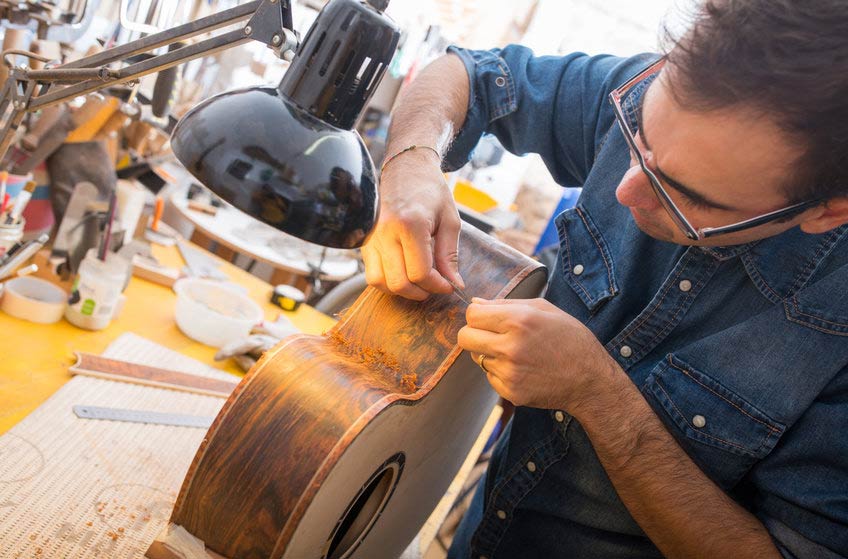
How To Become an Instrument Repair and Restoration Specialist
- Career Description
- Salary
- Career Outlook
- Career Path
- Experience & Skills
- Education & Training
- Additional Resources
- Sources
- References
Career Description
Instrument Repair & Restoration Specialist John says on a normal workday, “theoretically, I’ll go in and work on projects that are already here and field phone calls. I get a lot of people asking questions. (I actually spend quite a bit of time telling people not to do something.) [I spend some time] ordering parts.
“I like doing a lot of my work when the client shows up because I’d much rather take it, do it, hand it back to them and not have the instrument sit around my shop for three weeks. If I have projects, they’re long term projects; they’re not anything like a water key or anything like that. I’ll do that till I either have to go to a rehearsal or something’s good on TV.”
Repair Specialists fix instruments for players from all walks of life, from children who have just started taking lessons to accomplished Session Musicians, Concertmasters, Section Members, Section Leaders and members of Dance/Cover Bands, Show Bands, and Recording Groups. If the Repair Specialist is employed by an instrument shop, he or she may also work with the Music Store Manager, Instrument Sales Representative, and Music Store Salesperson. Self-employed Repair Specialists work on their own, either out of their home or in their own shop.
Salary
The average annual salary for an Instrument Repair and Restoration Specialist is $49,800. Salaries for Instrument Repair and Restoration Specialists range from $27,000 to $69,000.
How Repair Specialists earn income “will vary based on a bunch of things,” John says. “There are people out there who have flat rates. Some people have a flat fee of $100 and I think that’s crazy.
“I’m of the mind that if I put on a water key spring and it takes me two minutes and it costs me a dollar I’m not even going to write up a bill — because I know they’re going to come back. So much in brass isn’t parts; it’s dents and fixing things, which is good because I don’t have to have a lot of inventory. I usually take it by-the-hour but sometimes I kind of know a student has no money and I’ll cut him a break.
“Other people have obvious means and I’ll take extra time and make sure everything is pretty and shiny on their stuff because they like that. It’s not gonna play any better but it makes them feel good so that’s fine.” In many cases, Repair Specialists will work for a predetermined hourly rate instead of charging a certain fee.
Hey, what do you think about trying our new Music Career HelperMusic Career Helper really quick? It’s totally free and could help get your career moving fast! Give it a try. It’s totally free and you have nothing to lose.
Career Outlook
Instrument Repair & Restoration Specialists who work in music shops have set hours that align with those of the shop’s. Self-employed Repair Specialists are available on an as-needed basis. John says, “My shop’s in my house so I’ve gotten emergency calls on Sunday night at 9:30 pm, saying ‘I just got in from a plane and the TSA screwed up my horn.’ I say, ‘Come on over!’
“If somebody’s a touring musician, they need their instrument. To balance home life and stuff like that, I don’t keep hours where I’m absolutely here — because I might not be here. I might be going to a sporting event or to the store or whatever. So I don’t have absolutely fixed hours, but I do have extended hours. It gives me some flexibility, and the client, too.
“It’s a mix of professionals and weekend warriors. There are musician hours and the people who actually work [in offices] have hours that are very different. So if someone has to work, they come in after work or Saturdays or Sundays. Musicians don’t get up until 10 am at least so they tend to want to get here late, too.”
How frenzied a Repair Specialist’s daily schedule is depends on how many repairs are already on deck and the pace of work he or she likes to maintain.
John says, “I like to have a quick turnaround time. I wish more technicians would work like that, because so often when a kid brings a horn to a music store, the clerk will take it, put a tag on it, then it’ll sit on the floor till the repair person fixes it in five minutes.
“Then it sits around again and the horn’s out of the kid’s hands for two weeks. Kids don’t have backups like professional musicians and it’s the most important time for kids to learn.”
Career Path
Instrument Repair & Restoration Specialists generally begin their careers as Apprentices to more skilled technicians. After they’ve put in some time learning on the job and are confident in their abilities, they can strike out on their own. Career advancement then comes through building a large, loyal clientele and through alliances with prestigious clients such as a city’s orchestra or a well-known musical artist.
Before striking out on the job hunt, aspiring Instrument Repair & Restoration Specialists must already have a certain amount of knowledge and experience.
John advises, “I wouldn’t necessarily say a high school student would make a good choice to go out and start out in this profession. They have to be at least a really good college player because I don’t think you’d be good enough to help anybody otherwise — that being said, you could be really mechanically gifted and that’s fine.
“Some people say if you can’t make a career out of playing, teach. Well, if you’re not a very good musician, how are you going to teach music? People say the same thing about repair. When people say ‘this is my fallback’ well, go practice! Don’t besmirch what I do as a fallback. If somebody’s really interested in repair, go take a technical program and bother your local music stores till they hire you to clean out horns.
“Get on the internet, call technicians and ask them questions; you’ll soon find out which ones will talk to you and which ones won’t. You’ll have to ask. There are very few repair classes. It’s not like every junior college has an instrument repair program.”
If repair classes or a technical program are not an option for the aspiring technician, he or she should contact music shops or self-employed Repair Specialists to inquire about job shadowing or apprentice possibilities. After apprenticing for a period of time, they’ll be ready to begin applying to music shops for any available positions.
- “They should be absolutely competent in taking apart their own instrument. If not, that’s a great place to start. They should be able to maintain it, take apart all the parts and put it back together without worrying about it. Then they can work on other people’s instruments, and they can work on other instruments beyond what they play.
- If they have some workshop facilities, buy some instruments on eBay and experiment. [If a mistake is made], at least they haven’t ruined someone else’s horn. Once they realize how deep they are, maybe they realize it’s not a good idea, or they think ‘that was fun, let’s see what else I can do!’
- Always just figure out what you can do. Can you change a tire on your car? Can you change the oil? Can you change the water pump? If you can fix a water pump, maybe you have a shot at fixing a trombone or trumpet, but if an oil change is better left to somebody else, maybe you should find something else.”
Experience & Skills
Obviously, an Instrument Repair Specialist must have a high level of technical aptitude, but he or she must also have strong performance skills, and be familiar with instruments outside of his or her area of specialty. “They should be able to play their instrument at a high level,” John says.
“Because then I can empathize with what a professional player would want. If you’re an accomplished player, you’re going to understand what they’re talking about, and if you’re like ‘well it works, take it,’ it’s not going to work out for you.
“Always be willing to learn more, and look outside of instrument repair for inspiration and tools. I like going to woodworking shows, gun shows, anyplace with anything mechanical because there’s always a tool there where I’m like, ‘Oh, look at that!’ Because I can use that.
“Any kind of training they can get is always good, but it’s generally catch-as-catch-can. There are all kinds of stuff on the internet. You can read a book; I doubt anyone’s ever become a Repair Tech because they read a book, but you can always say ‘I know how to do this and the book says to do that’ and figure it out.
“You have to absorb [knowledge] from every direction. You can’t go, ‘Well, I finished my class and now I know what to do and I’m done. You have to look at it from every direction and know your goal.
“Another thing is knowing when to stop. When you get anything somebody started to fix and they went too far and broke something — whether it’s a parent or a player — that’s the reason they’re not a technician. Then I see what they did and I have to fix not only the first problem but what they broke, too. It’s about being sensitive to what you need to do without causing any damage.”
There are certain commonalities in personality John sees among Instrument Repair Specialists; many enjoy being by themselves, which makes sense, as repair can be solitary work. “I think there’s probably a good portion of them who are probably kind of loners or curmudgeons as they get older,” he says.
“There’s nothing wrong with that, as long as it doesn’t get in the way of things. On the flip side, I like talking with people and that’s one of the reasons I like having people here when I’m working on their horn. Some people hate having people around when they’re working but I like catching up and talking to people. You don’t necessarily have to be a loner, but it seems like quite a few are.”
“One of the most important traits a Repair Technician should possess is confidence. John says, “You want to be pretty self-confident when you start tearing into somebody else’s instrument. If you’re overly cautious, it’s going to be torturous for you to start working on someone else’s horn.
“You know the old redneck saying ‘hold my beer and watch this?’ You kind of have to be like that. You can’t be timid, like ‘gosh, I don’t know what to do.’ Certainly, the customer doesn’t want you to say that. You have to be confident about your abilities and if you exceed your abilities you have to have the resources to figure it out.”
Education & Training
Since instrument repair and restoration requires specialized knowledge, finding an academic program that teaches the necessary skills can be a challenge. Fortunately, the best way to learn is through hands-on experience.
John’s advice to aspiring Instrument Repair Technicians: “I would make sure they have a mechanical background or mindset before they even think about it. A lot of people say ‘I’d love to do repair.’ I say, ‘Can you change the oil in your car? No? Then maybe it’s not for you.’ So many times they just don’t have any mechanical abilities; you can explain it to them but they’re just not going to get it.
“If I was going to tell anybody to get training I’d tell them to get training in everything, not just brass, not just woodwinds, not just strings. Say I’m a trombone player — that doesn’t mean I can’t be a good repair person for strings, etc. You don’t want to limit yourself and you might need the income from different interests.
“I’m not saying you should only fix what you play but you don’t know till you try, so I’d learn about anything.” He adds, “If somebody is good at anything mechanical you can always go to a music store and apprentice. You can go to the technical schools like Red Wing [Minnesota] or Renton [Washington state]. Those [schools] have no entrance requirements and it’s a basic, basic entry-level [program].
“What you’re doing is getting prepared to become an Apprentice. I can’t think of any schools where you come out ready to be a full-fledged decent technician, and on top of that, if you want to do any kind of specialty [you won’t learn that there]. You’ll always be learning on the job and that’s part of the fun. It’s just like being a player.”
Additional Resources
“There’s the National Association of Professional Band Instrument Repair Technicians,” John says.
“They have requirements to join but they also have outreach programs, resources available to technicians, and support. They have a magazine and suggested rates and that kind of stuff. (By and large, the bottom-end people don’t go to NAPBIRT and the higher end don’t [either]. It’s usually the middle ground. If you’re really good at repair or you’re not very good, by and large, you’re wasting your time.)
“You can learn a lot by looking through the Ferree’s catalog. They sell a lot of repair tools but will send [the catalogs to] people who aren’t Repair Technicians.
“Most instrument repair places won’t sell their tools to people who aren’t [professional] technicians. It’s that thing that if you don’t know what you’re doing, don’t do the damage. They don’t want people doing damage or building weird Frankenstein horns.
“There’s a guy named Dan Oberloh up in Washington; he has a lot of really amazing repairs he’s done and he’s put them on his website. That would be a good place to look for brass. I don’t know anyplace for woodwinds but I’m sure there are some.”
Sources
John
John is a Southern California-based Instrument Repair & Restoration Specialist. He owns his own shop and specializes in brass repair.
References
- 1Multiple. "Average Instrument Repair Technician Hourly Pay". PayScale. published: Nov 13, 2019. retrieved on: Dec 17, 2019